Arcitile + H&E Smith
A Space Between Arcitile + H&E Smith
Date May 2023
Location London, UK
We believe in a better way of doing business, one that’s about delivering the best results while fostering positive relationships from the moment we place an order to the final installation
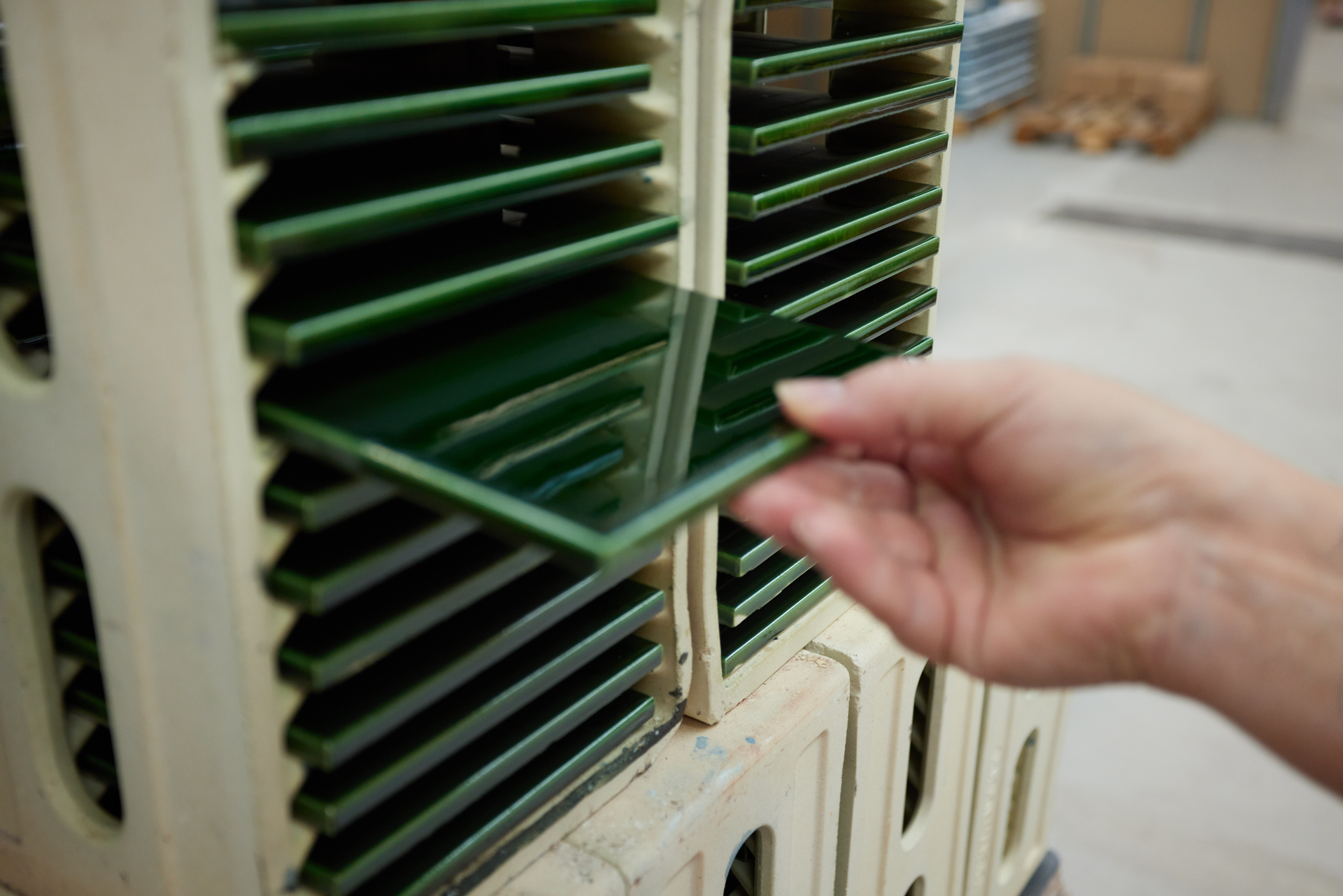
We have more than forty years’ experience between us at Arcitile, and one thing we’ve learnt above everything else is the indisputable power of collaboration. To us, this involves finding the most talented people out there; working closely and transparently with all suppliers, tradespeople, and clients from start to project completion. That’s what led us to starting Arcitile in 2017.
One of our close partners is H&E Smith, based in the North West. With fewer miles than overseas manufacturers, we’ve been able to forge a very close connection with the team there; just as our base in Clerkenwell gives us easy access to our clients in the capital.
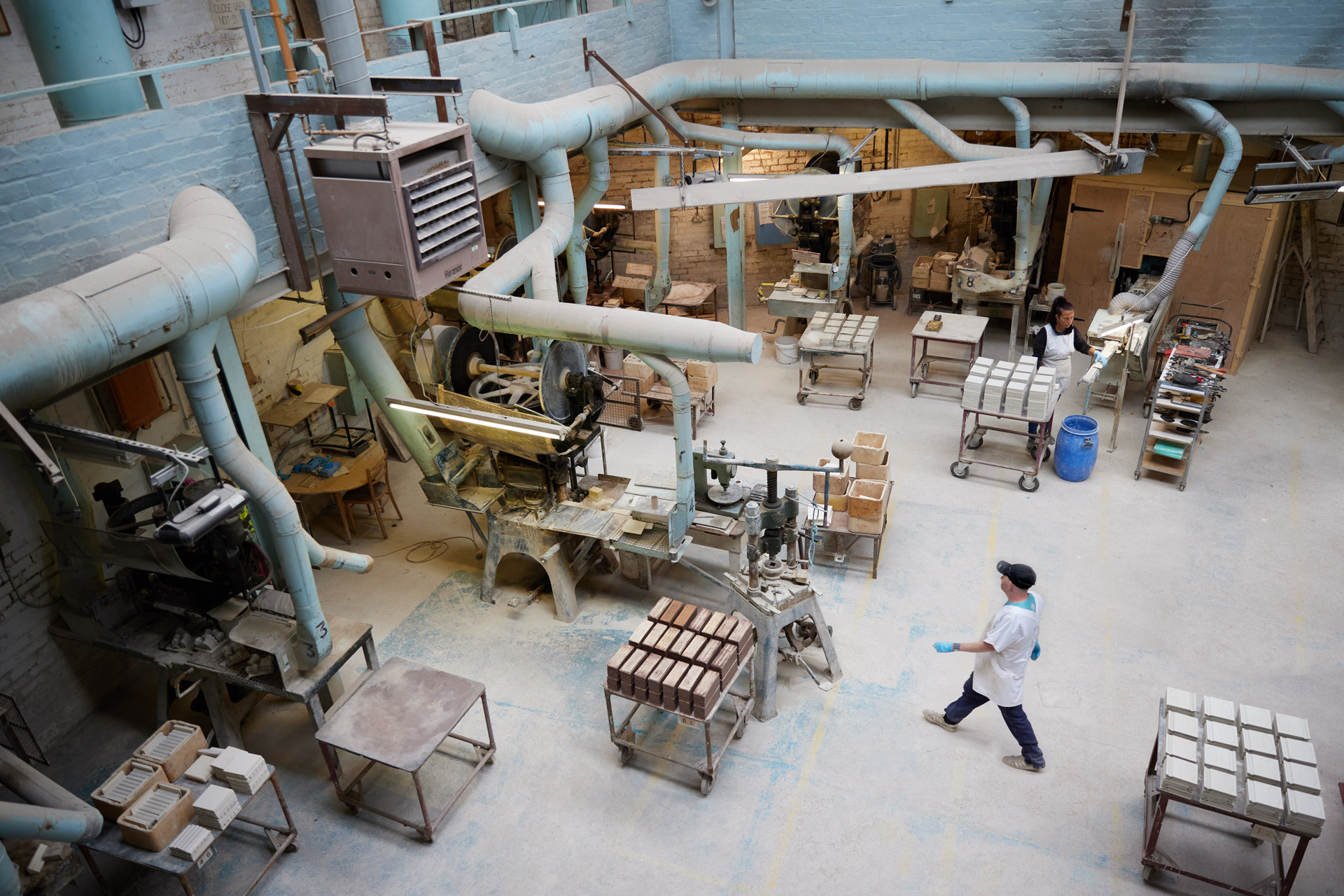
Hands-on care ensures every tile is honed to perfection
While we aren’t manufacturers ourselves, we have scoured the country and continent for the best makers out there. Over our years in the industry, we have fostered great connections with manufacturing partners who excel at producing beautiful, quality tiles. What we pride ourselves on is taking our clients’ ideas, no matter how complex, and explore the many possible ways of bringing the designs to life. Designs that may have started as an idea sketched down on paper, that then gets briefed into the right factory and gets installed by the right team for the job. Often the lead time in the programme means that we must be sure we can rely on partners who deliver on time, which is why it’s essential to know and trust our suppliers.
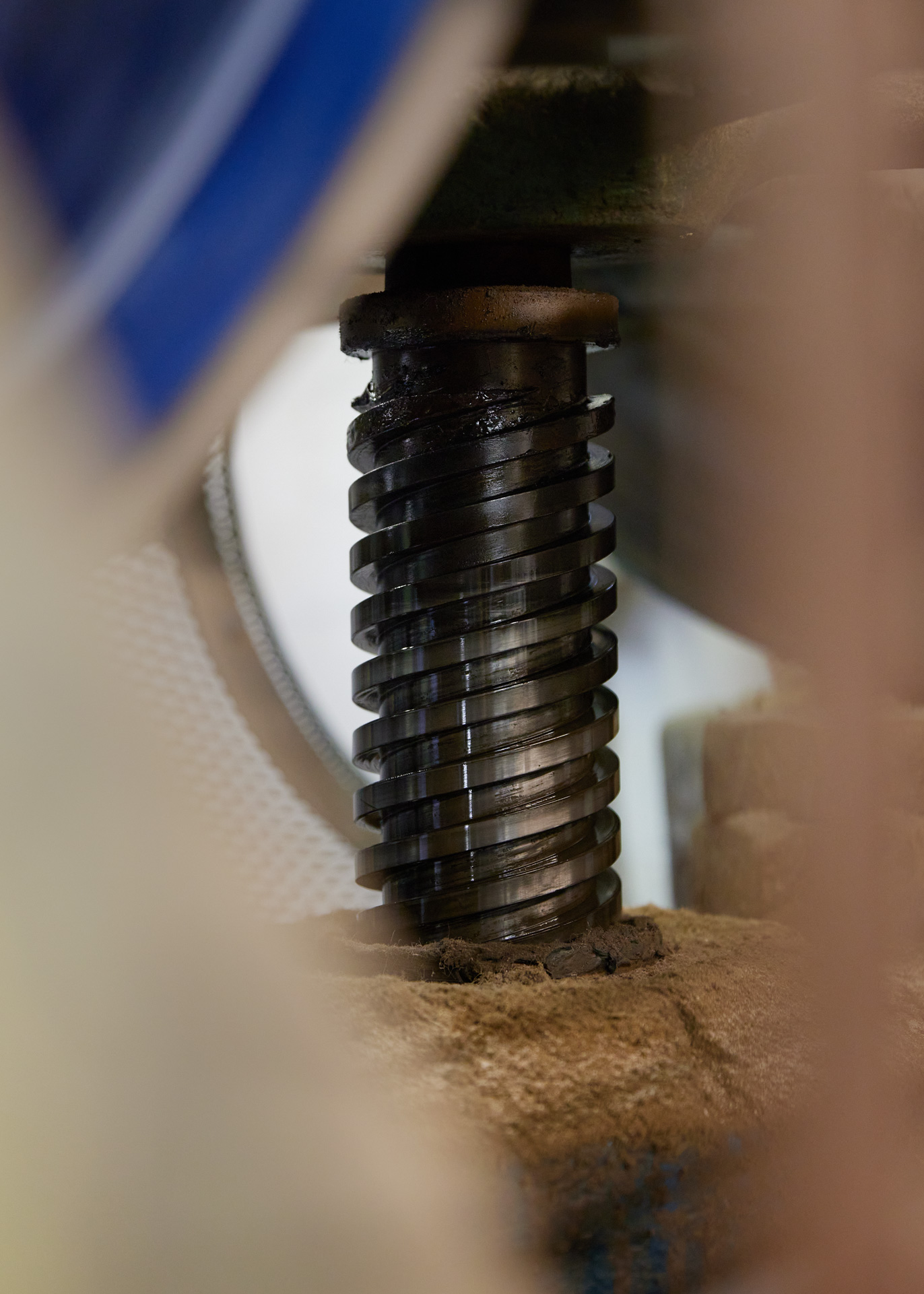
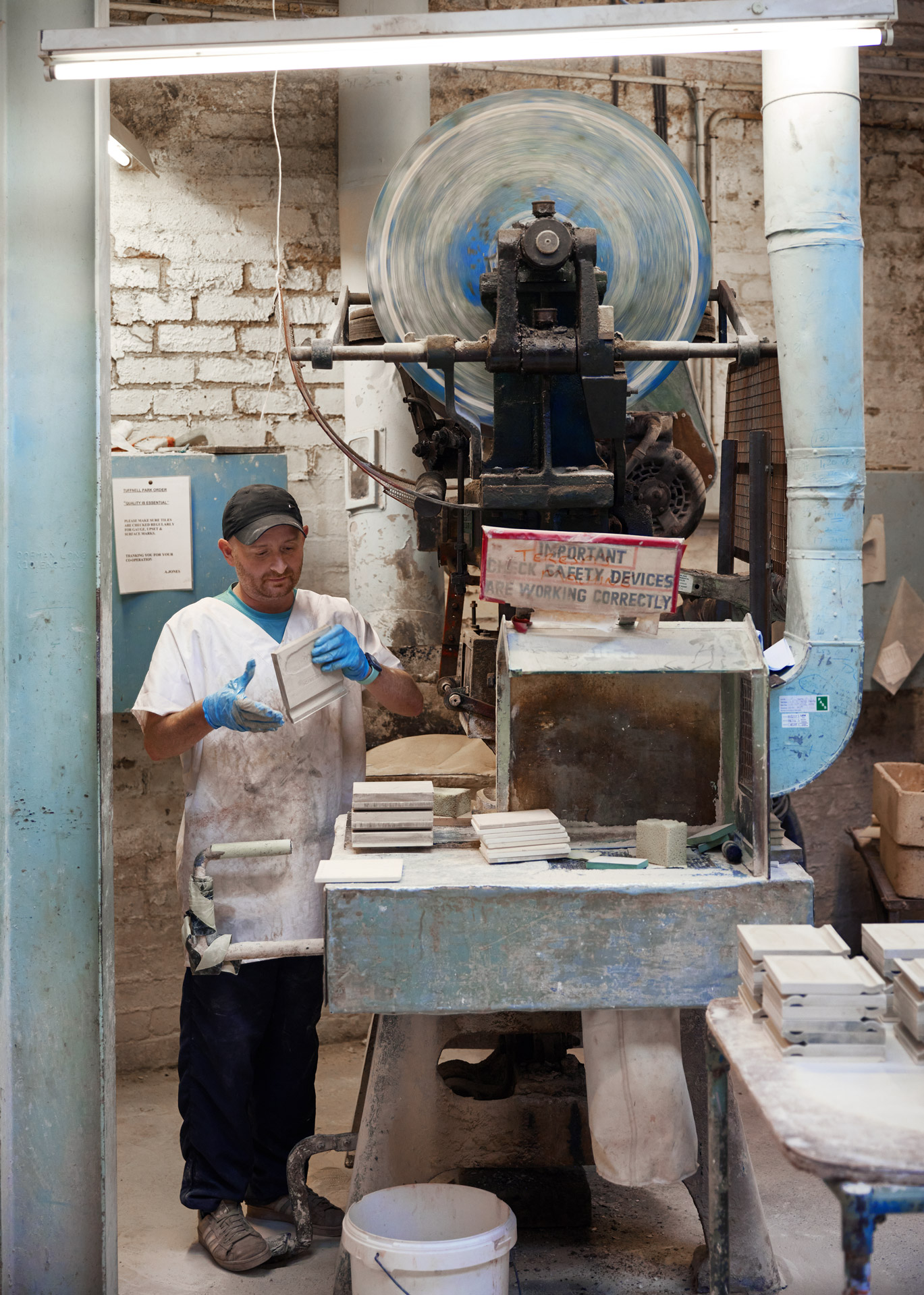
H&E Smith are pioneers of British craftsmanship, manufacturing bespoke tiles since 1926. We were invited back to their factory in Stoke-on-Trent to bear witness to the intricate craft of tile making. The area is synonymous with pottery manufacturing as far back as the 17th century, thanks to the local abundance of clay and coal. While much of the manufacturing base has now disappeared, H&E Smith maintains production at its factory in Hanley, the industrial hub of Stoke-on-Trent. The factory as it stands today was constructed in 1960, though many traditional techniques employed inside date back over a century, and have been passed down through three generations of this family business. Starting out manufacturing refractory glazed tiles for fireplaces, the company later began to make traditionally crafted English ceramic wall tiles.
Upon entering the factory, you are immediately aware of the century-long artistry housed in this quiet corner of the North West. What strikes you most is the careful balance of the traditional with the modern; a perfect marriage between human and machine that sees the factory’s craftspeople work in harmony with decades-old machinery to create tiles that are beautifully timeless.
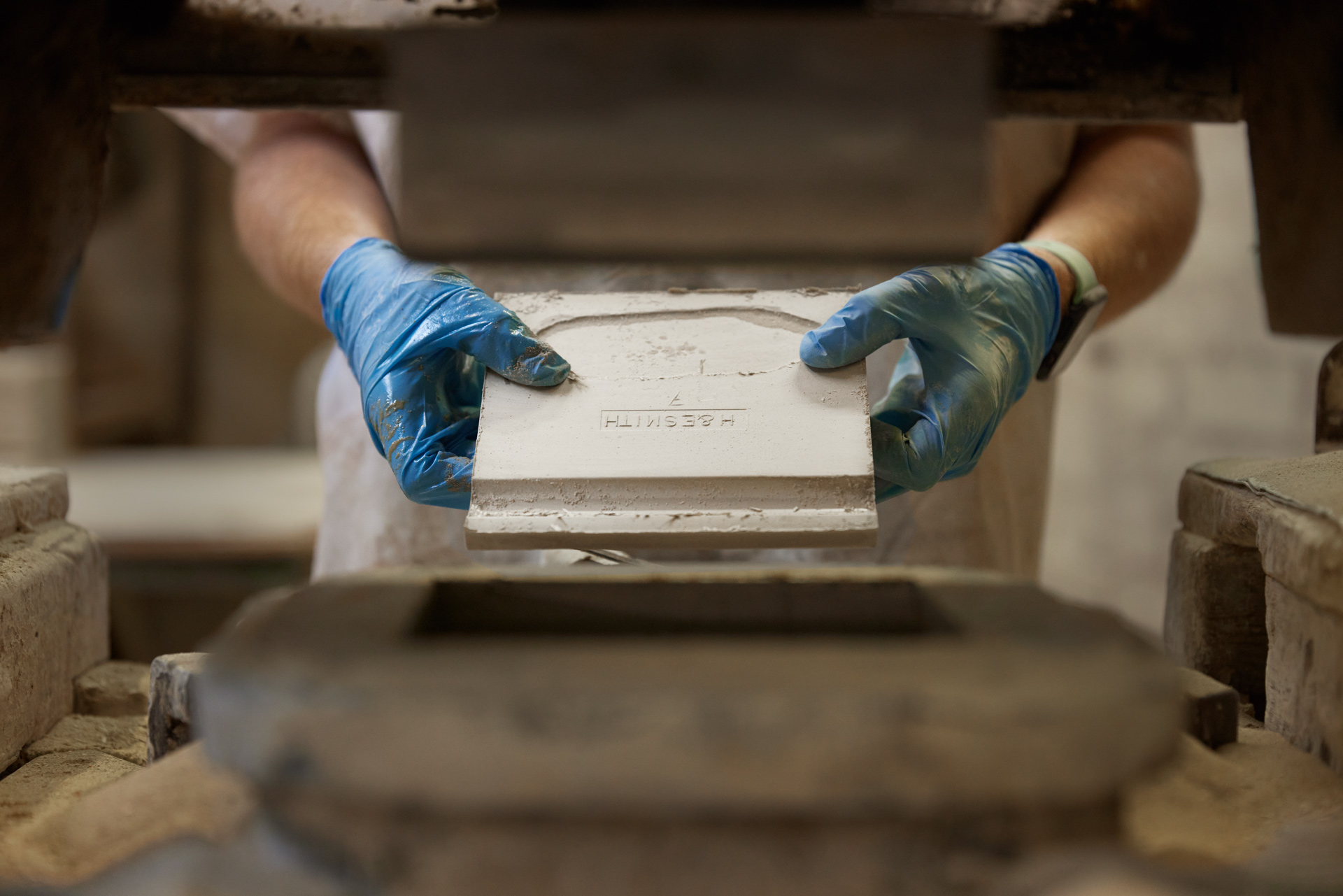
Timelessness is right at the very heart of tile specification and is why they are an increasingly popular choice of material for architects and designers. That combination of colour and texture options as well as durability is hard to beat. Tiles are also increasingly viewed as a sustainable surface solution since they are less likely to need replacing during the life cycle of a building.
What’s incredible about age-old factories like H&E Smith’s is that they often fall in line with sustainability practices by the very nature of their manufacturing processes. As you move around the factory, it’s hard to miss the lack of any form of waste, even down to the very ‘dust’ that forms the inception of each tile.
In our own way, we try to contribute to sustainability by looking at how we can harness technology and cutting edge systems to ensure the seamless success of each project.

The dust is pressed in a semi-automatic process dating back to the 1920's
The tile making process itself begins inside H&E Smith’s beautiful cavernous 1960s factory where the light floods in and the mezzanine level provides a perfect picture frame for the activities below. The highly experienced team of craftspeople work closely together, starting with a dust made of clay, silica, alumina and feldspar which has been sprayed to add in moisture.
The dust is then pressed in a semi-automatic process dating back to the 1920s by simultaneously lowering a lever and pressing on a foot pedal to add pressure to the dust in the mould. The tile forms are then dried to remove as much of the moisture as possible.
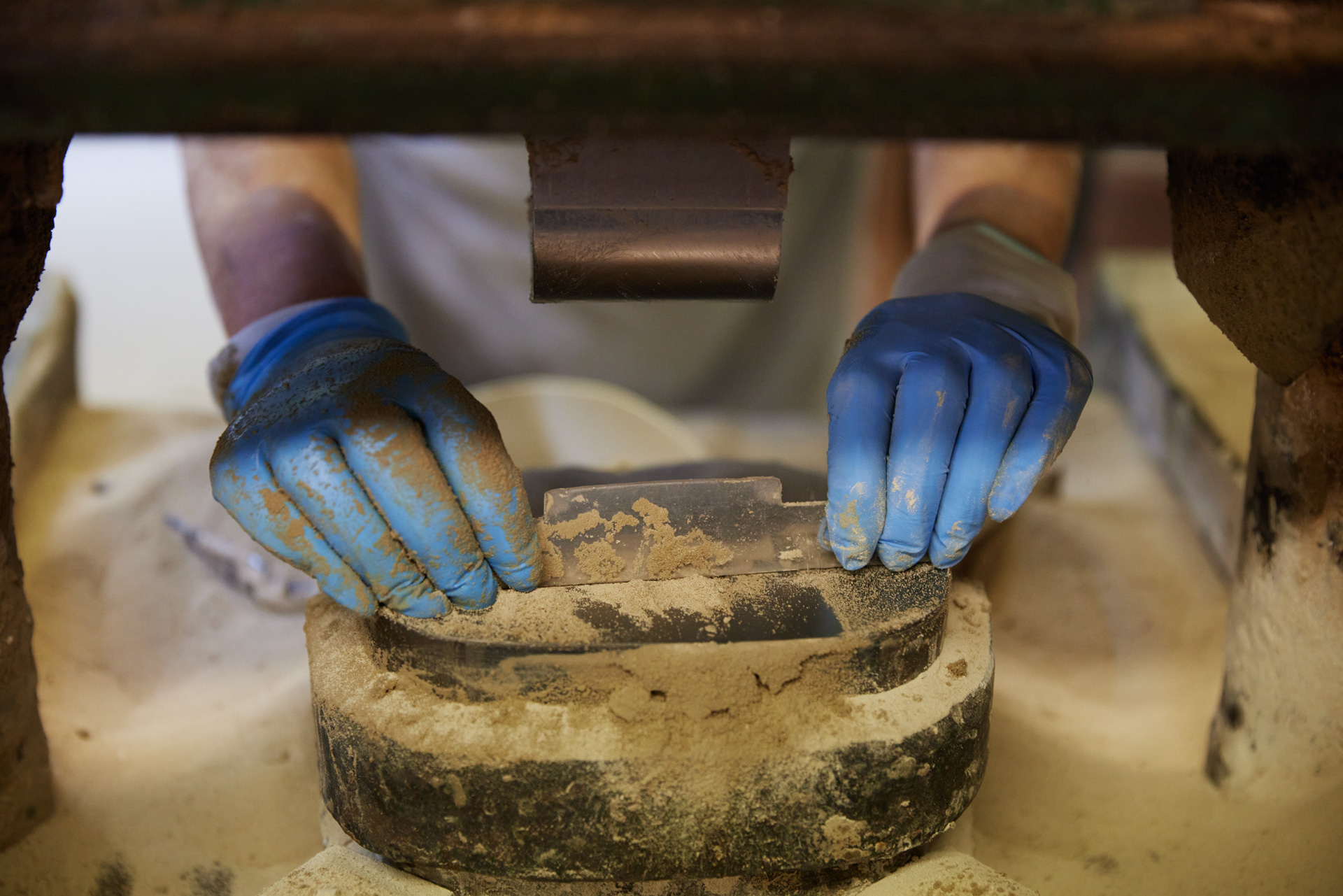
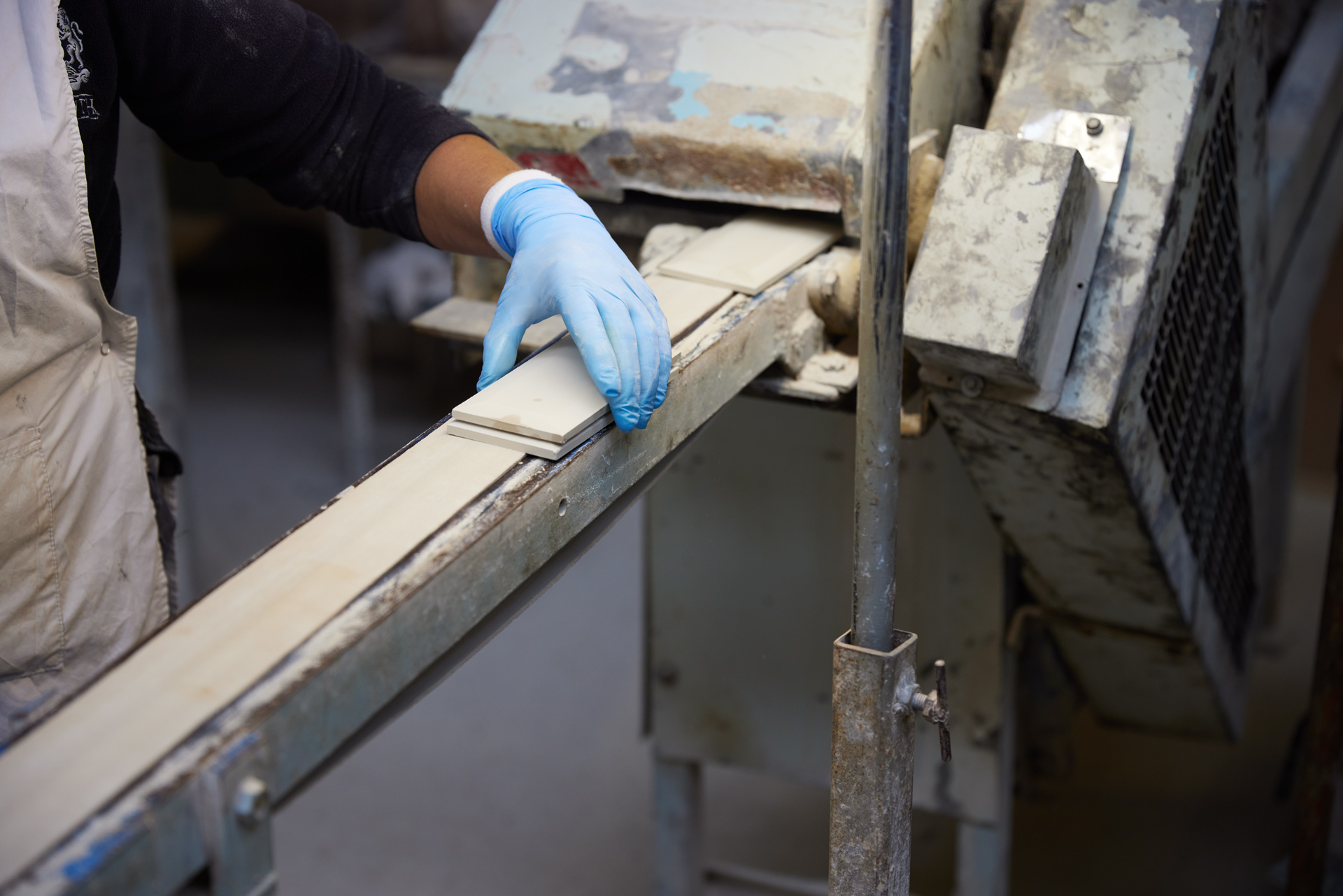
If the tiles are going to be glazed, they then roll on to the ‘dipping line’ where a liquid consisting of a glass derivative called ‘frit’ as well as dyes are applied. This not only gives the tiles their colour, but the resulting glossy surface of a ceramic glaze also protects them from staining and wear and tear.
From the dipping line, the glazed ceramic tiles are carefully placed in ‘cassettes’ which then go into the kiln to be fired at high temperatures. It’s this firing process that gives the tiles their rigidity. Once the tiles have cooled and undergone quality inspection, it’s time to package them up ready to be used in an interiors scheme.
A hero of these traditional methods of tile-firing is Fred Smith, managing director of H&E Smith. As the third generation to run the company he talks passionately about the real craft of making tiles, from the methods used to produce the tiles and the pressing in the making shop to the glazing and firing. To Fred, what comes first and foremost is people. Each of the craftspeople housed in the factory have been there for decades and are at one with the machinery and with the resulting tiles. “We’re like a family here,” he says. It’s all about the people when it comes to selling the tiles too, “We have found the best route to market is to engage directly with architects, designers and people who specify our products.’
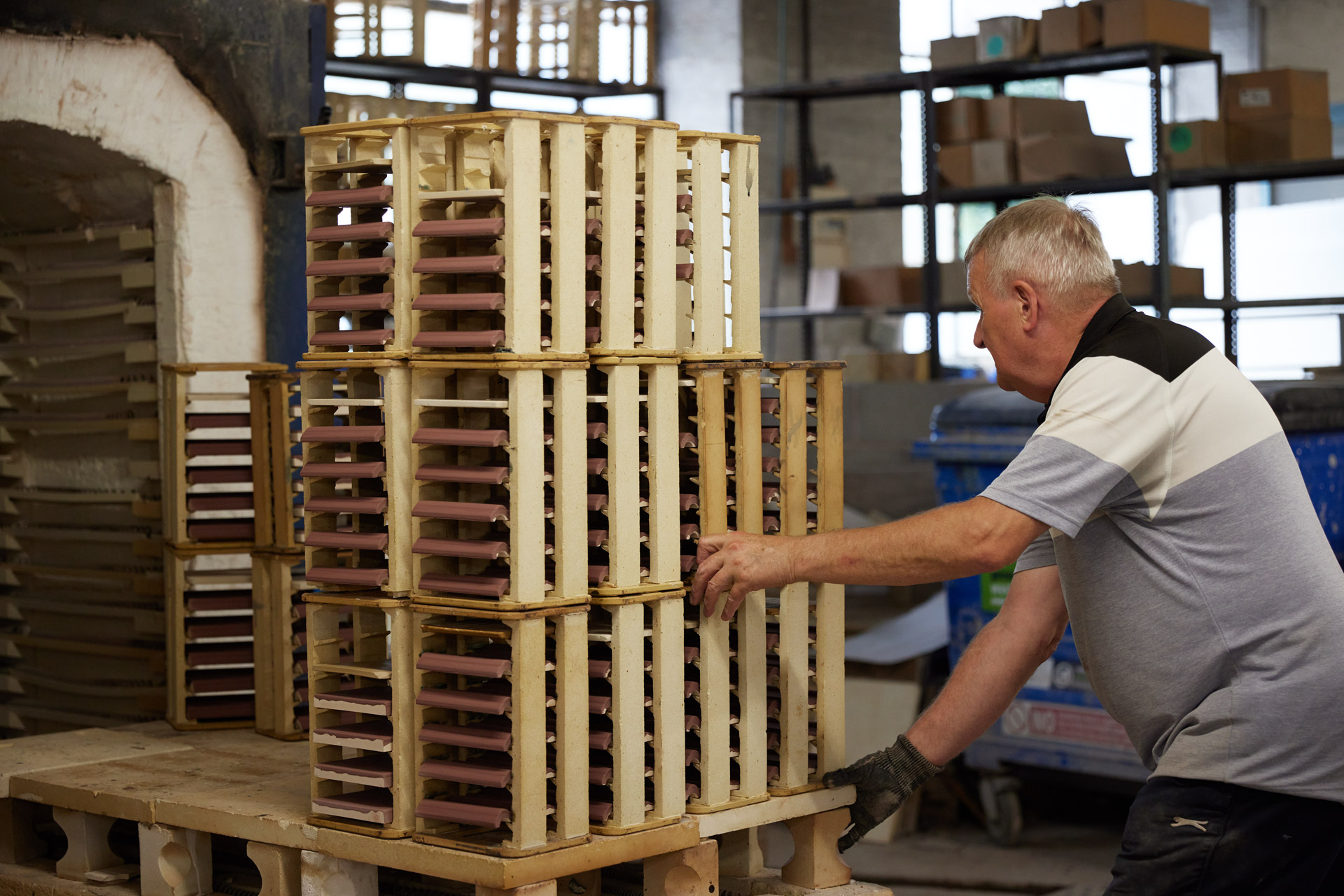
H&E Smith has produced tiles for countless projects in the fashion and retail sectors around the world, as well as supplying specialist ceramics to the London Underground since the mid-1980s.
It was this stellar heritage as a quality producer of Victorian tiles which made them a natural choice for Shropshire House, an Art Deco redevelopment in central London. Once extensive preparation works and overboarding had been completed, we wrapped the lift lobbies in brilliantly green glazed Victorian metro tiles. To respond to this very bespoke brief and to achieve the desired finish and thickness of tile quadrant, we went through a painstaking process of cutting and polishing the edges of the tiles. The result is a bold combination of texture, colour and curve running from floor to ceiling across six floors of this archetypal Art Deco building in the heart of London.
This collaboration with H&E Smith is just one example of how we bridge the gap between design intent and beautiful realisation; what we call ‘the space between’.
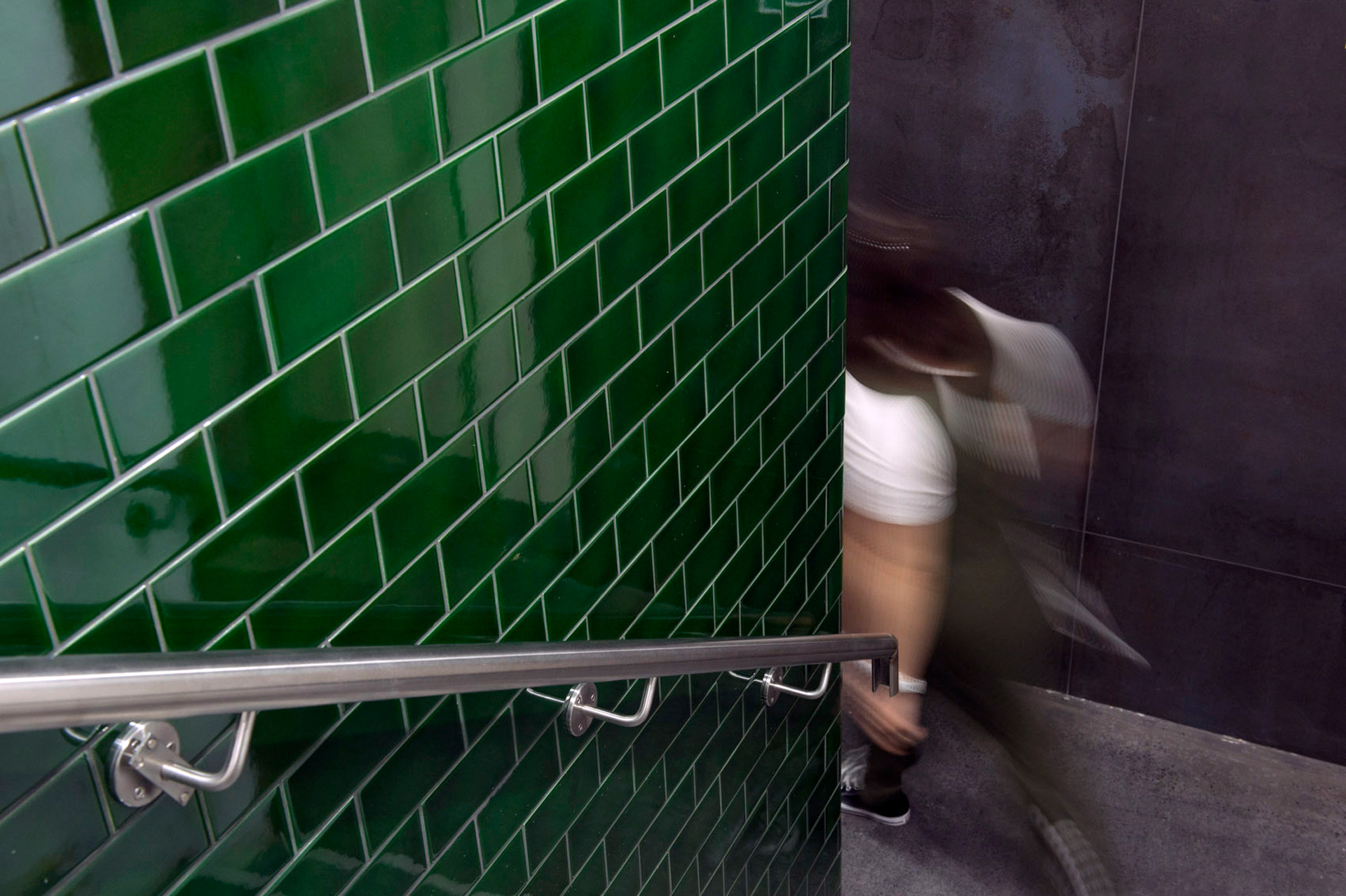
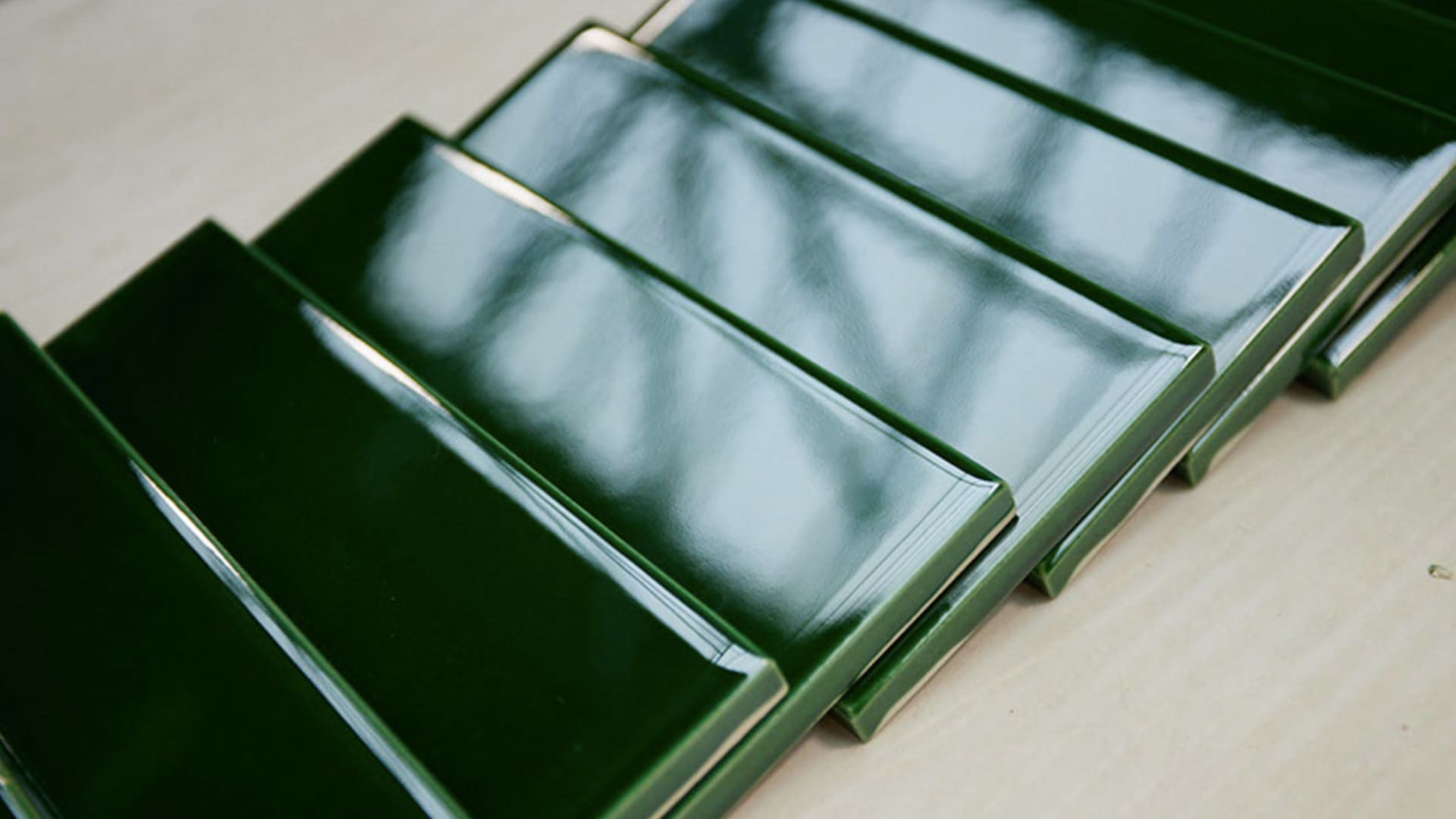
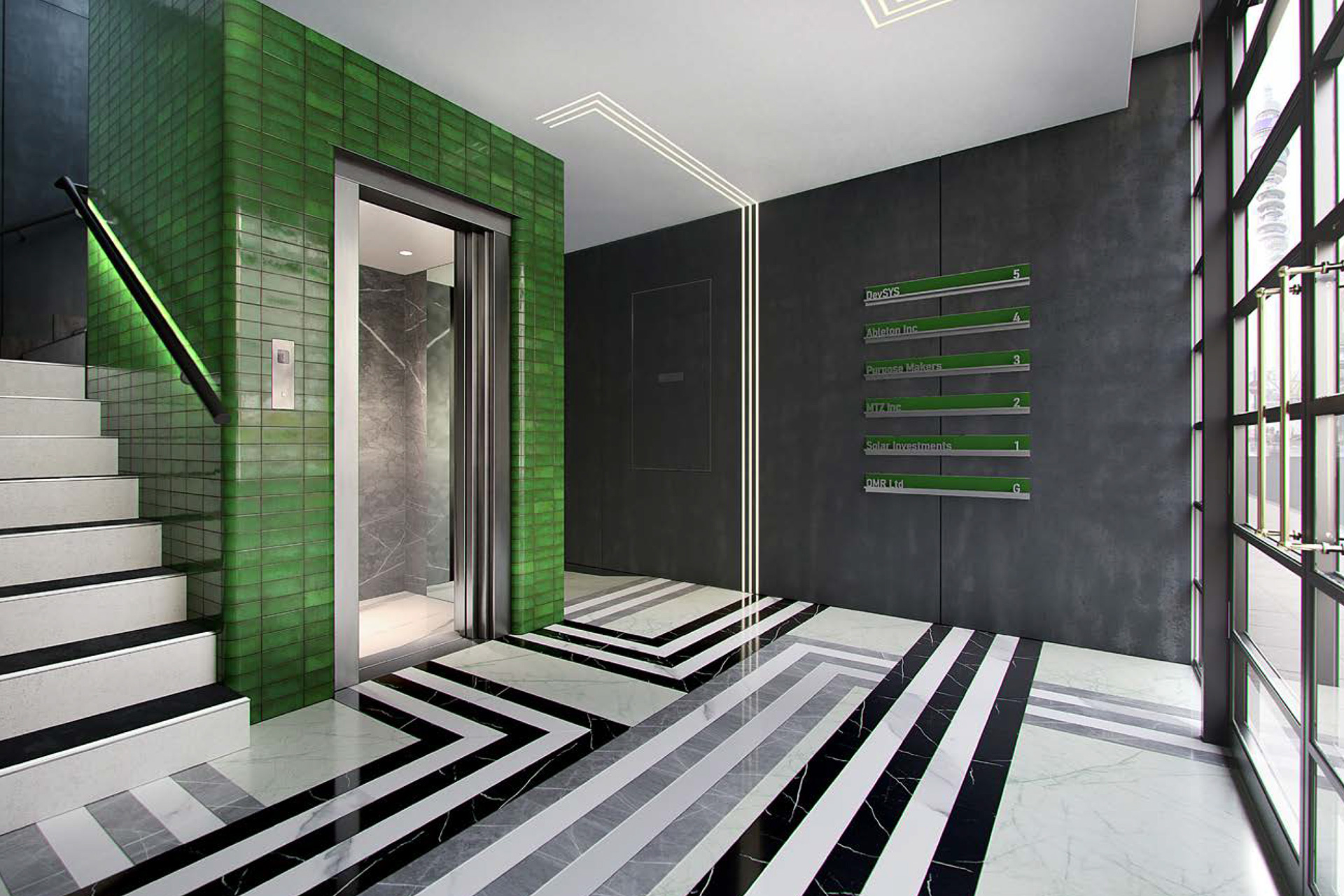
A Space Between
The Arcitile Journal
Edition 1
Arcitile + H&E
Smith Winter 2023
H&E Smith
Fred Smith,
Managing Director
Karen Hancock,
Marketing Executive
Architect
Hambury Hird Design
Main Contractor
Signature London
Photography
Leigh Anderson
Words
Helen Parton
Concept + Design
TM
tm-studio.co.uk
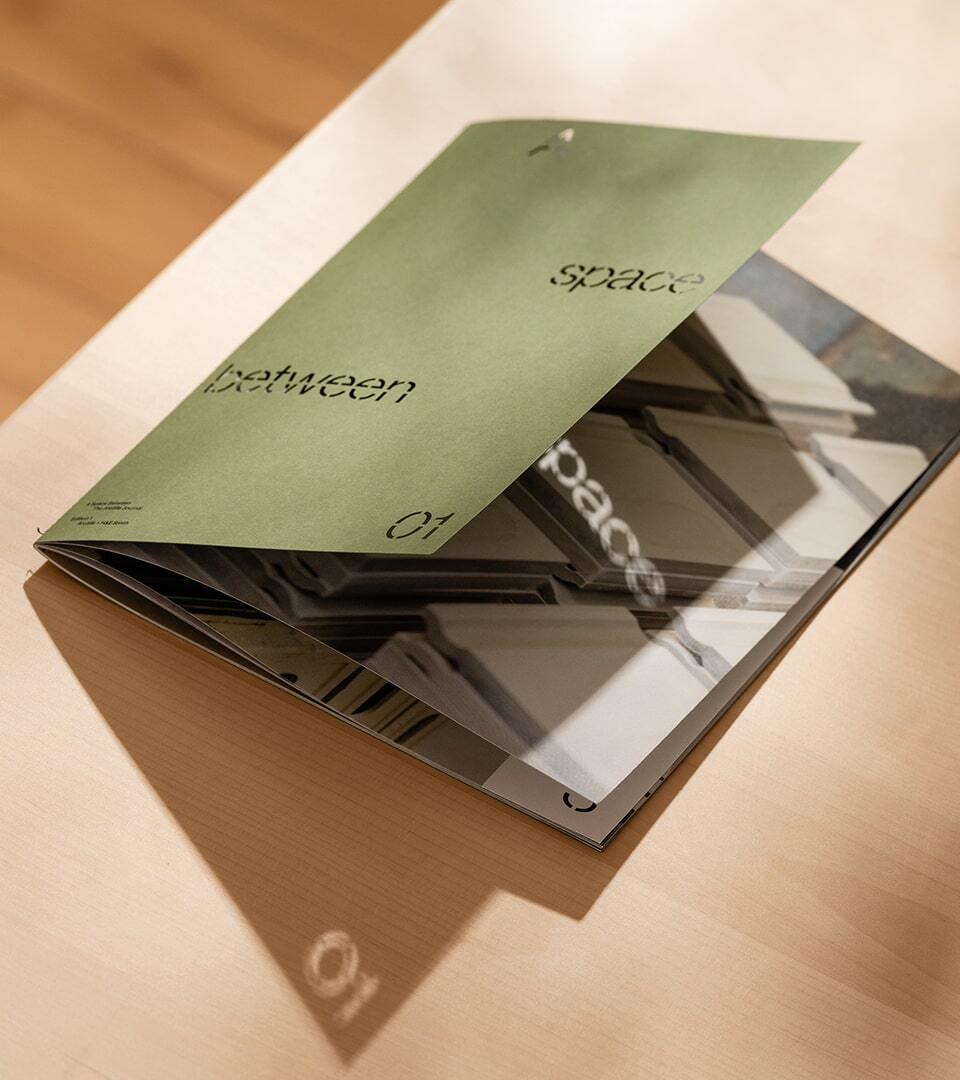